ANNUAL SHOWCASE AND FORUM 2024 – HOUSING INNOVATION
Best brains showcasing building innovations to help solve our housing crisis
A bricklaying robot, a prefabricated demonstrator pod, a modular retrofit façade to reduce energy consumption and a two-bedroom rapid deployment home – these were just some of the housing innovations on display at Monash University’s Caulfield Campus.
They were part of the Building 4.0 CRC Annual Showcase and Forum 2024, which took place on Wednesday 19 June 2024. This year, the event focused on housing innovation, with some of the best brains in the building industry showcasing prototypes, products and processes that will help resolve our national housing crisis.
Building 4.0 CRC CEO Prof. Mathew Aitchison has deemed 2024 the year of the solution.
“We have brought together significant demonstration projects where industry, government and the community can experience first-hand the building innovations created and share insights,” he said.
The Hon. Ed Husic MP, Minister for Industry and Science and the Hon. Josh Burns MP, Member for Macnamara visited on Thursday 13 June for a preview of the Showcase.
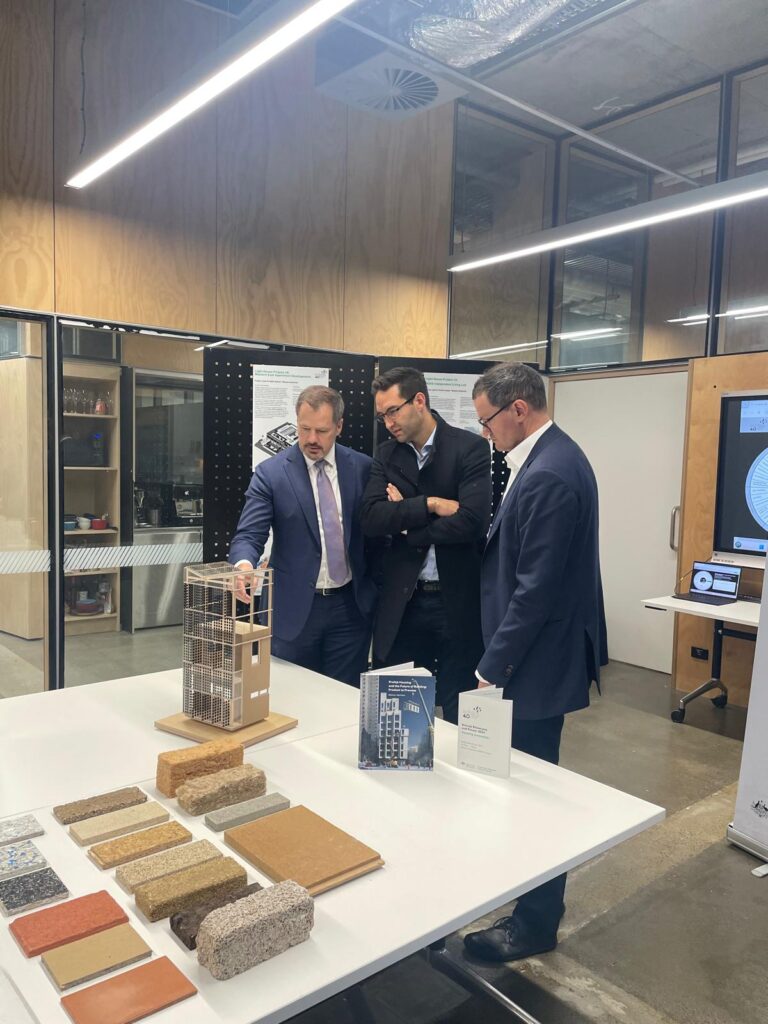
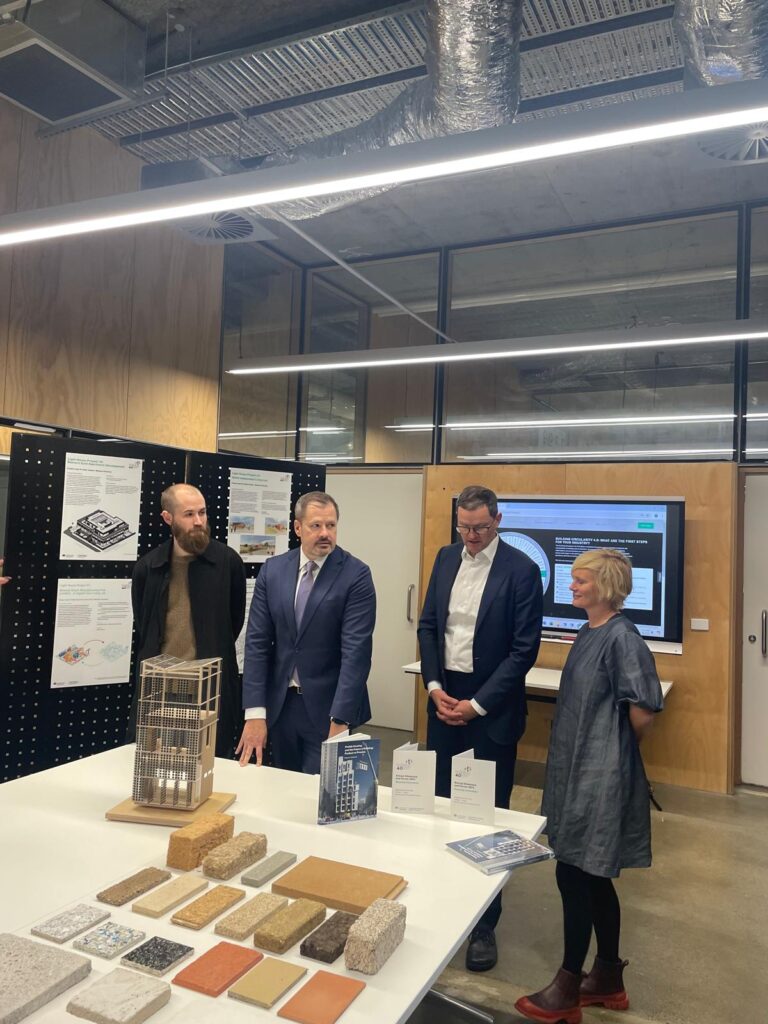
Keep reading for a wrap up of the day’s activities.
New ideas in housing
In a panel session chaired by Building 4.0 CRC Research Director, Prof. Chris Knapp, industry, government and academic thought leaders discussed more solutions to Australia’s housing issues:
- developing housing that meets the needs of residents as well as the environment
- seeing housing as a product that allows some adaptability to meet residents’ social and cultural needs
- encouraging consistent regulation
- increasing funding for social housing.
Our thanks to Alexandra McRobert (Homes NSW), Tara Goldsworthy (Fleetwood Australia), Prof. Mel Dodd (Monash University) and Jeremy McLeod (Breathe Architecture).
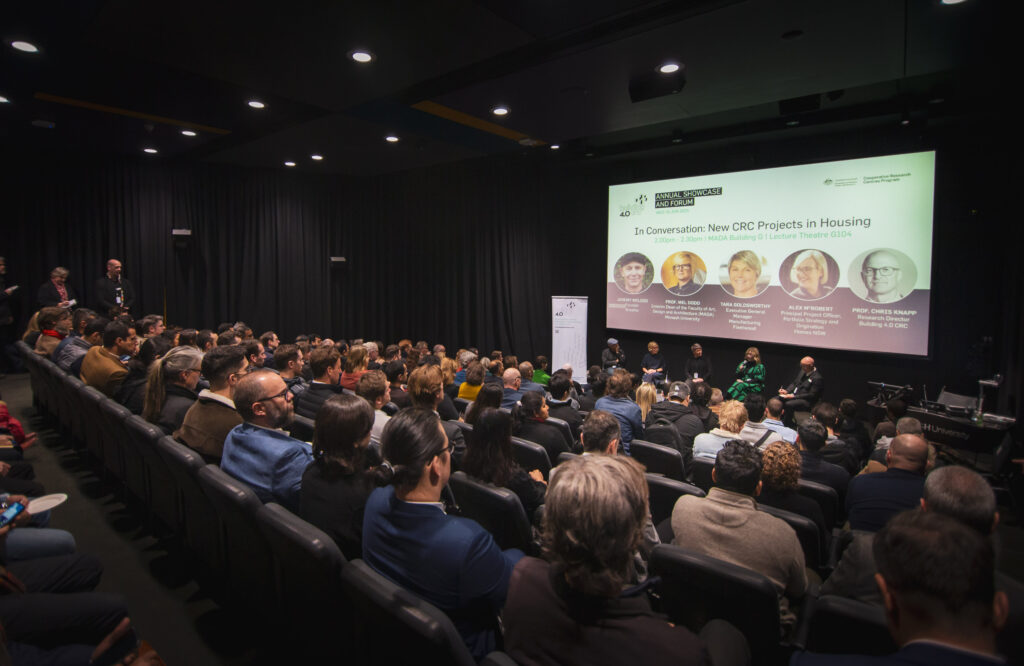
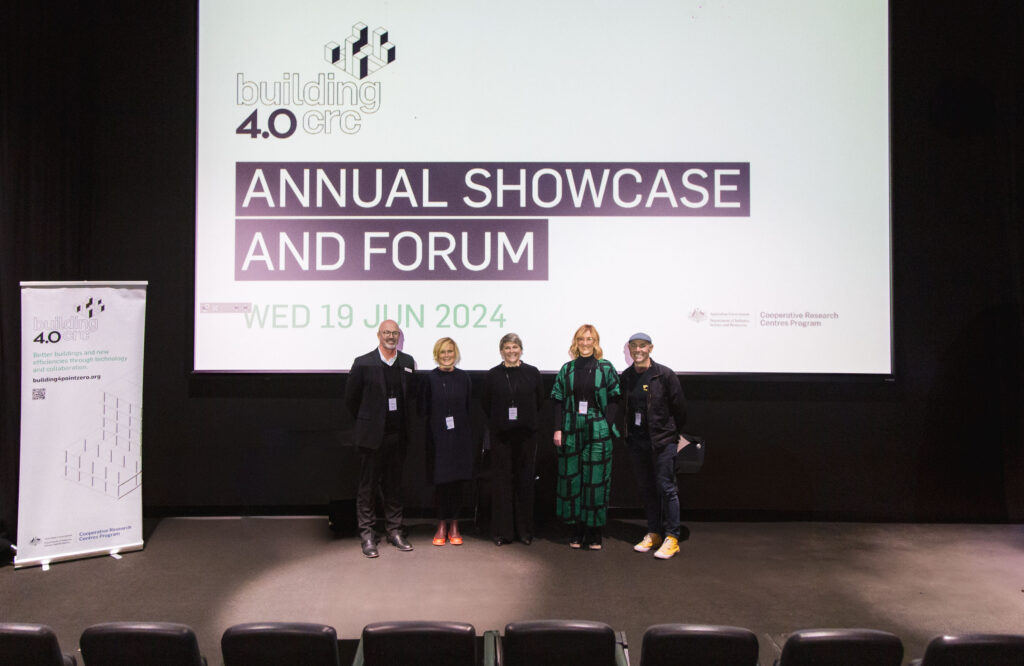
Modular housing solutions
A highlight of the showcase were modular housing solutions that can provide temporary and permanent housing solutions quickly:
- Candour’s prefab platform is a suite of customisable prefabricated building components that make the core of a building – the floor, walls, roof and façade.
- Monash University’s ‘kit-of-parts’ offers temporary housing in disaster-affected areas that can be expanded and extended to become permanent.
- SPACECUBE’s 45m2 2-bedroom Rapid Deployment Accommodation module is customisable and configurable, yet requires minimal fit out.
- XFRAME’s lightweight demountable timber framing is manufactured offsite and radically reduces building times.
- Developed by the Office of the Victorian Government Architect, Future Homes comprises ready-made architectural designs and a purpose-built planning process that facilitate medium-density infill in Victoria.
- ZERO Homes have developed a net positive homes – series built, fully electric homes that produce twice as much energy as they use.
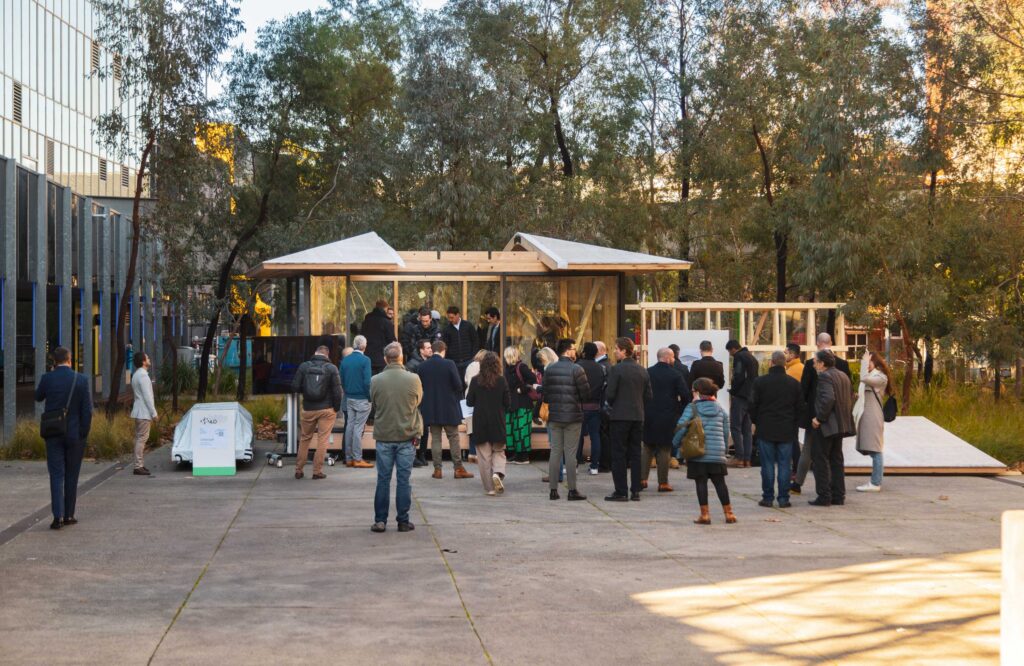
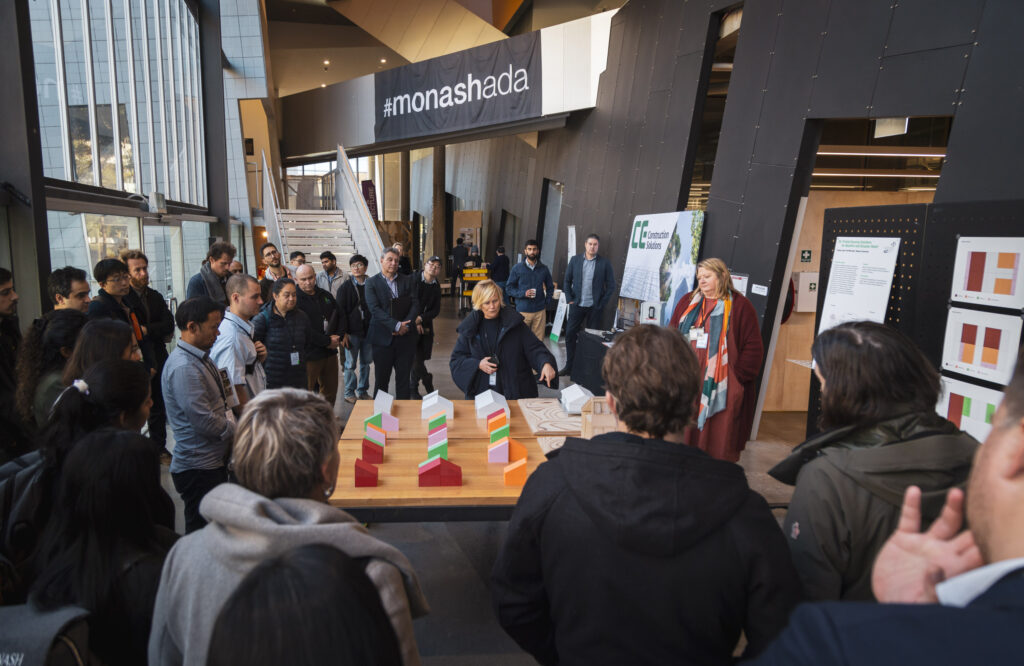
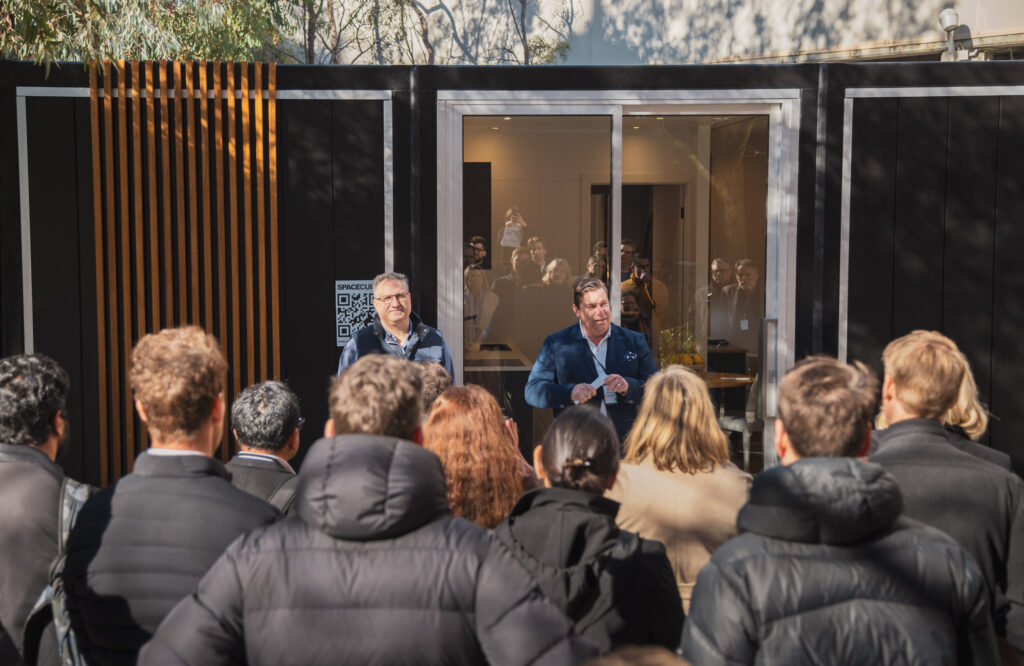
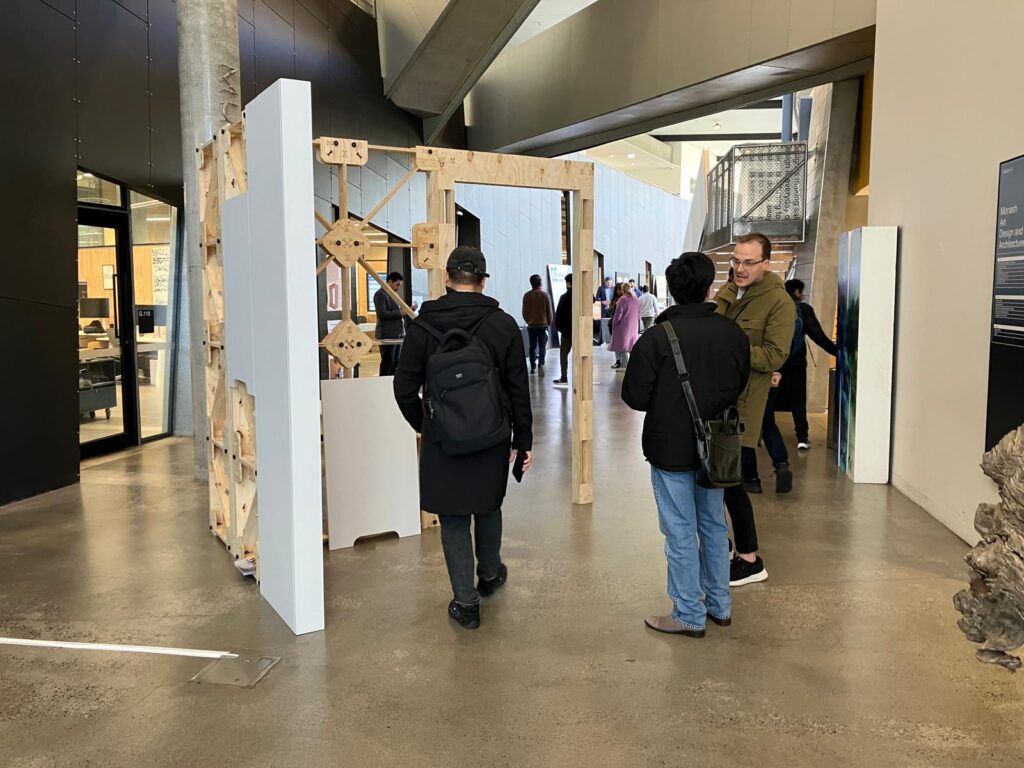
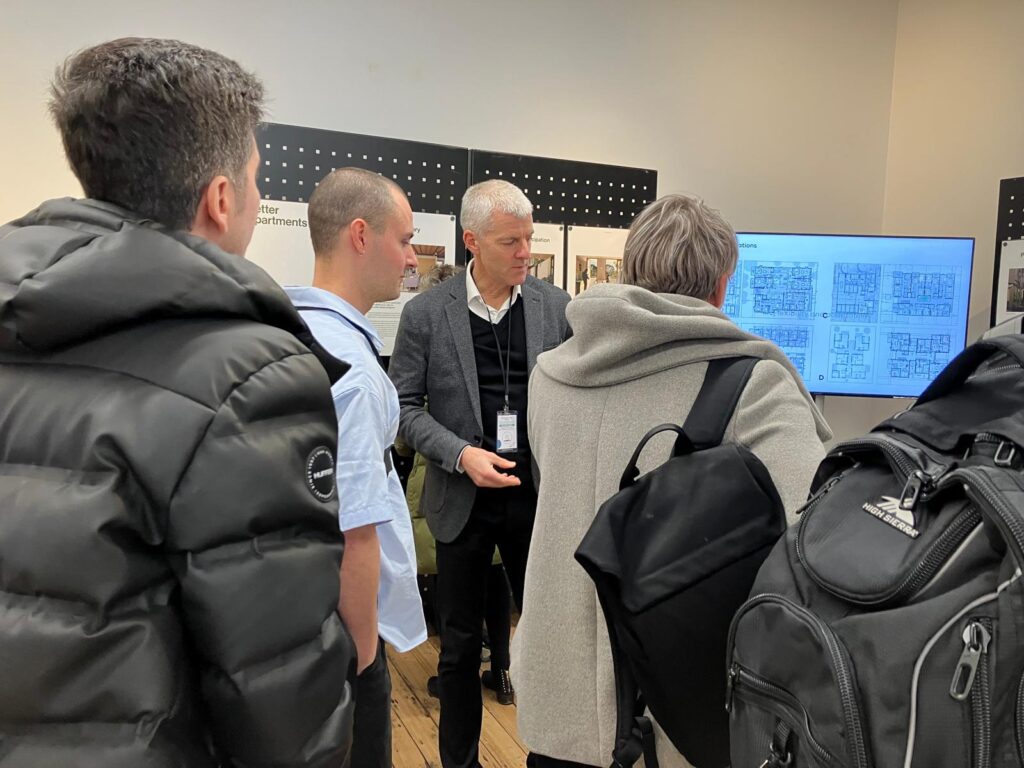
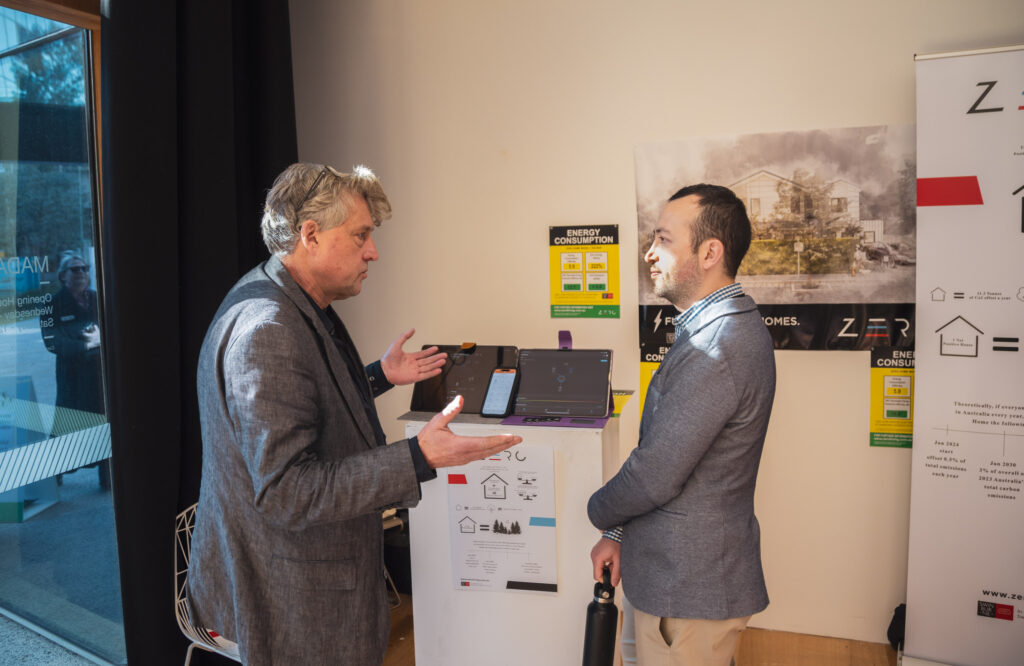
New building components
Also on display were new building components that deliver multiple benefits: lower cost, improved performance and better environmental outcomes. Examples include:
- Finding Infinity’s prefabricated integrated wall that improves energy performance and lowers supply chain risk
- Finding Infinity’s Carbon Positive Mass Timber Construction combines cost-effective, pragmatic, practical initiatives that are commercially viable and scalable
- Monash University’s new approach to improving the acoustic performance of light gauge steel frames to reduce noise in multi-residential buildings
- MASSLAM’s and Sumitomo Forestry’s mass timber bearing connection that makes timber mass construction fast, strong, safe and sustainable
- earth building materials that need less energy for heating and cooling (developed by the University of Newcastle, University of New South Wales, Earth Building Association of Australia, Earth Building Solutions, MudTech and Integrated Biotecture)
- CE Construction Solutions’ CarbonCure concrete that embeds CO2, enhancing the concrete’s strength and reducing the amount of CO2 released into the atmosphere.
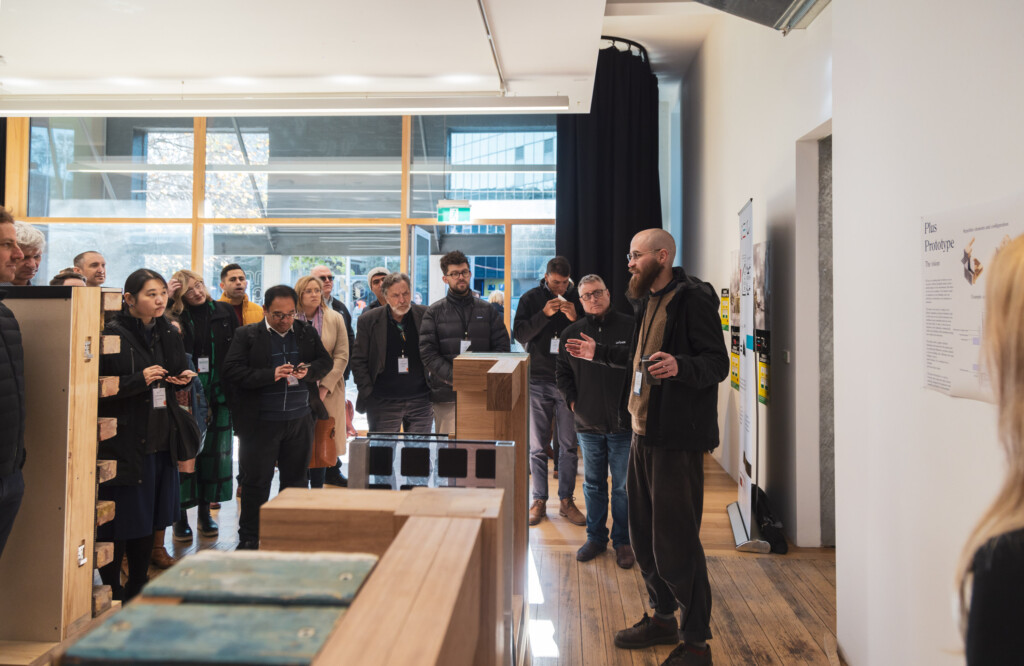
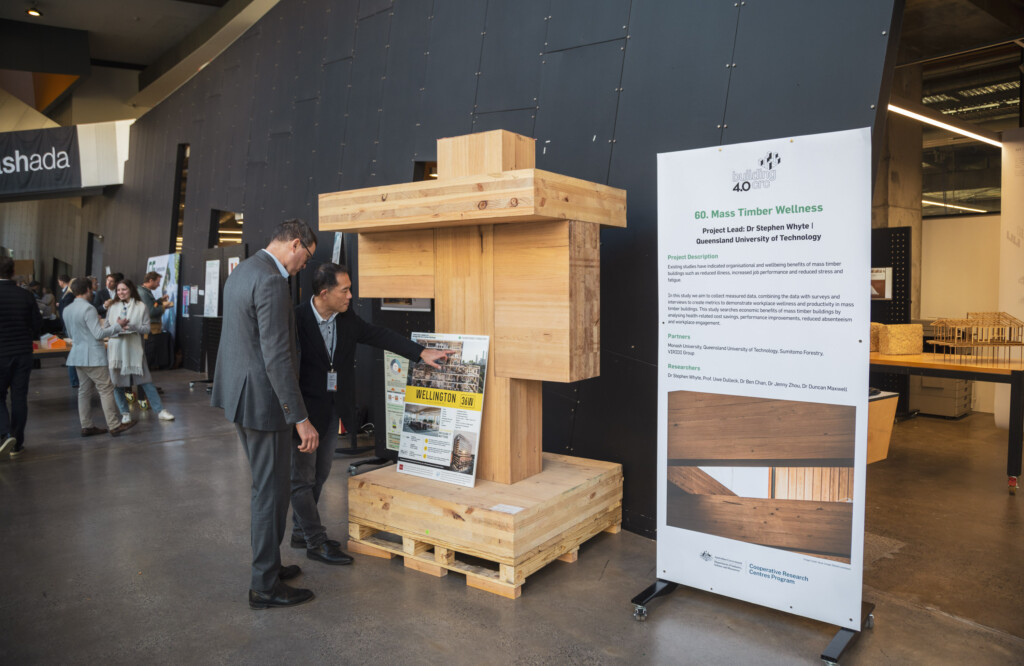
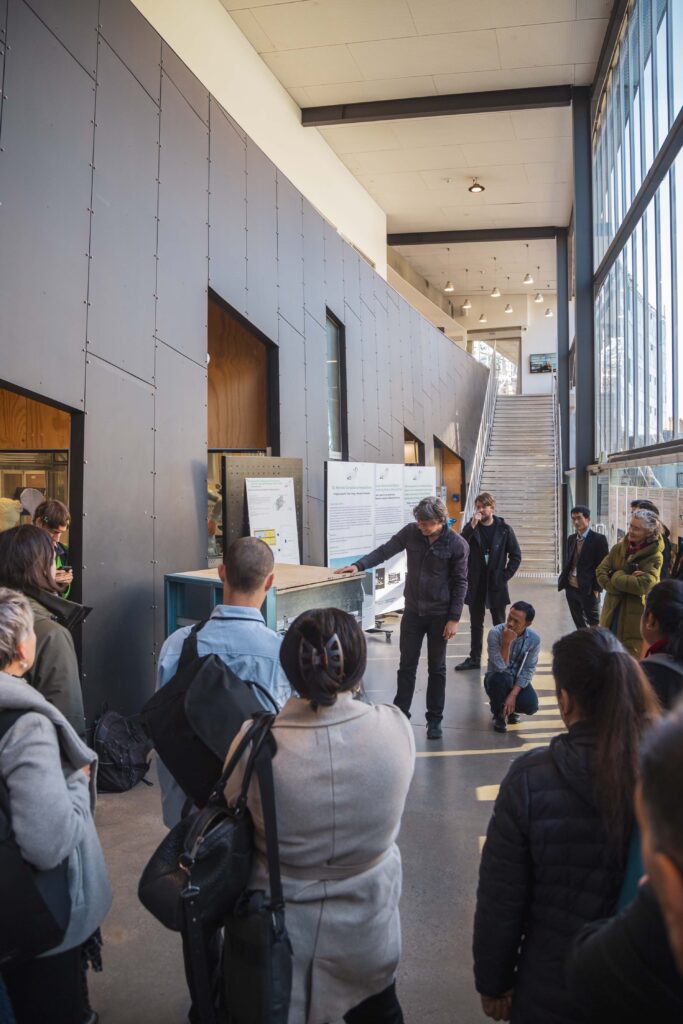
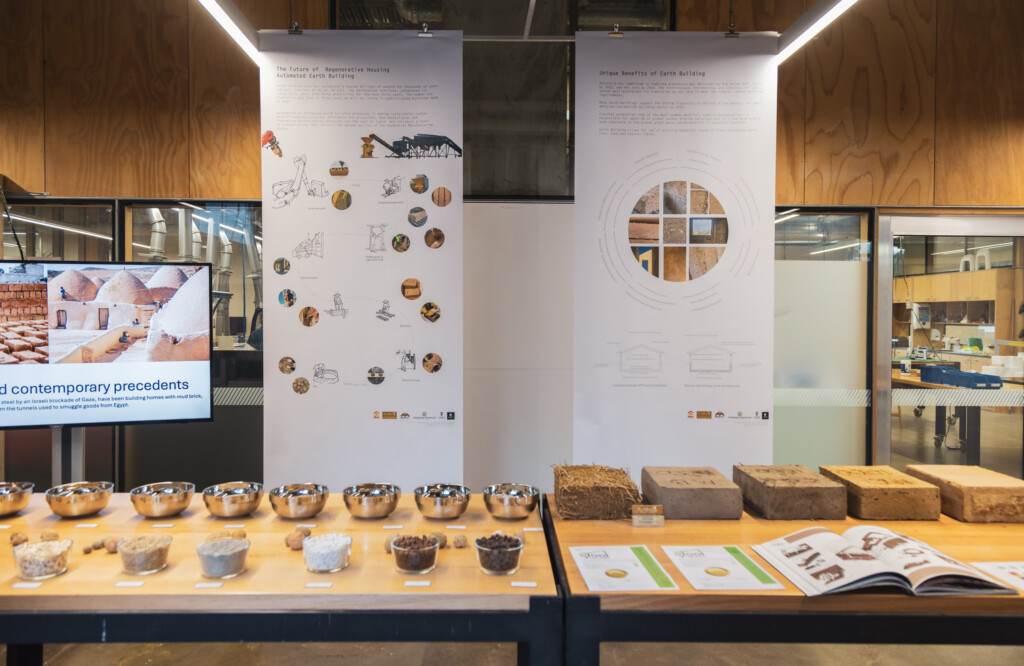
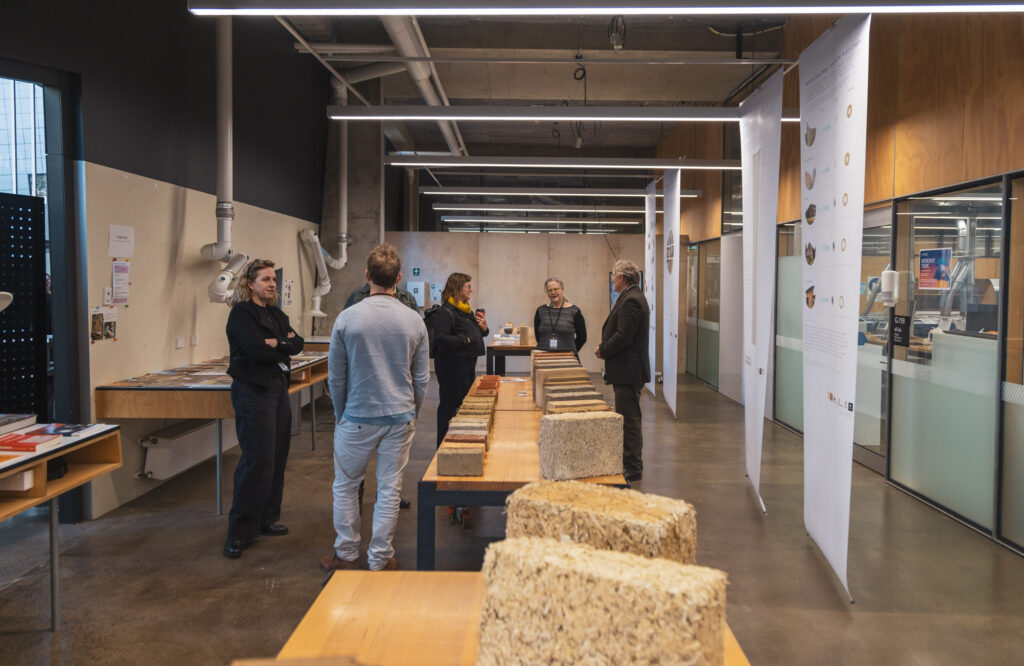
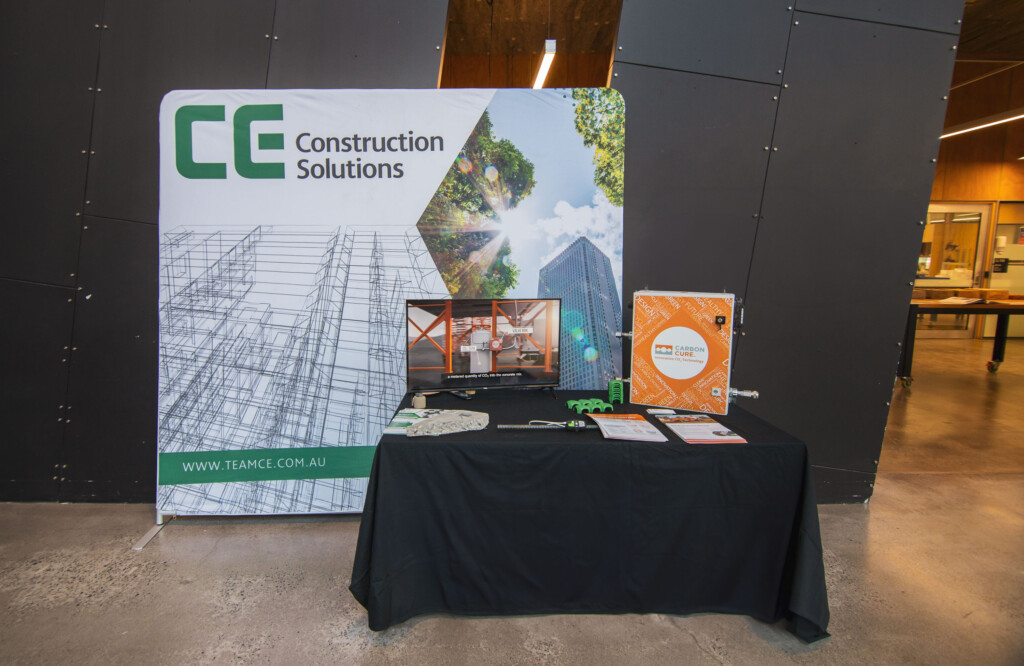
Platforms and processes
Innovation in building is not just about new components and new built form. A key element is moving building from project-based to product-based, and looking at ways to improve supply chains and processes.
Disruptors at the Showcase demonstrated organisations that are doing building differently:
- The Brickworks Mule Robot can pick and lay bricks with precision, increasing the efficiency of building brick walls.
- The Verton SpinPod 7.5 is a hands-off approach to lifting and orienting loads on construction sites that is both safer and more efficient.
- PT Blink’s construction software and marketplace allow flexible, offsite manufacture and onsite integration of buildings, to deliver faster, safer, better, less waste construction solutions.
- Bond University’s plywood panel system use a glue-only fixing system that eliminates the need for conventional fasteners.
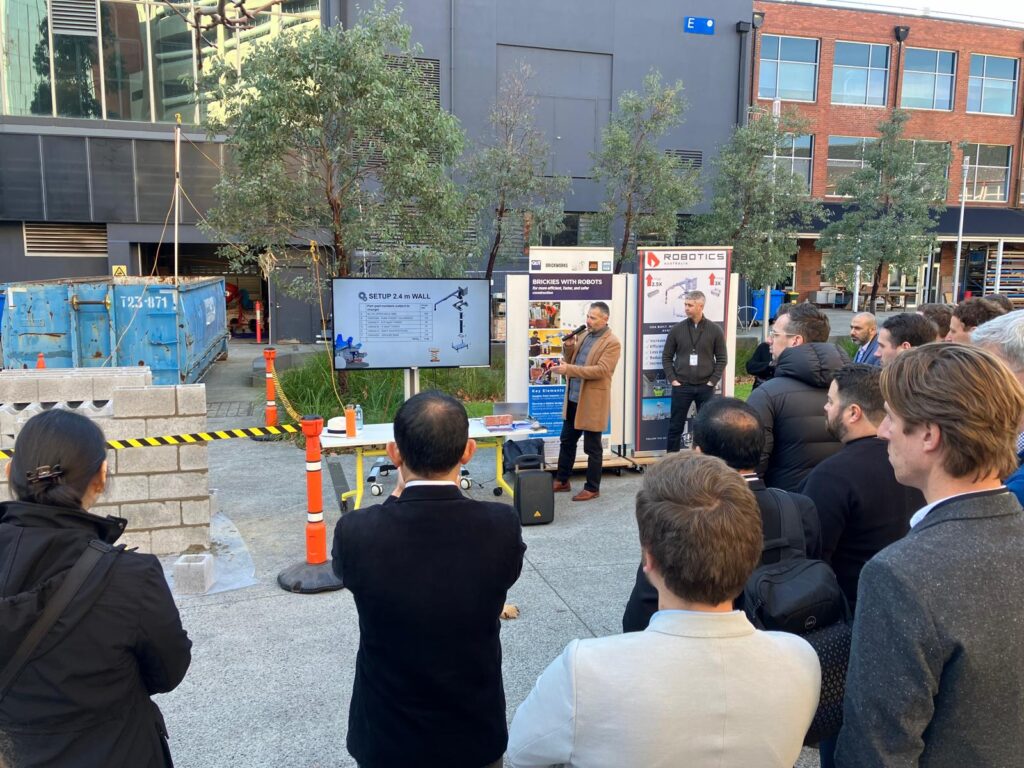
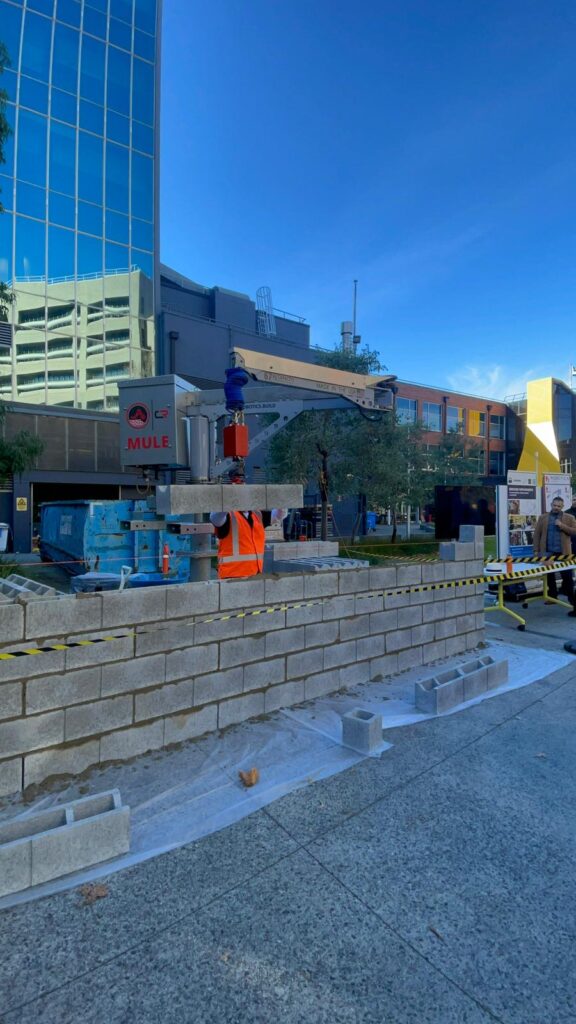
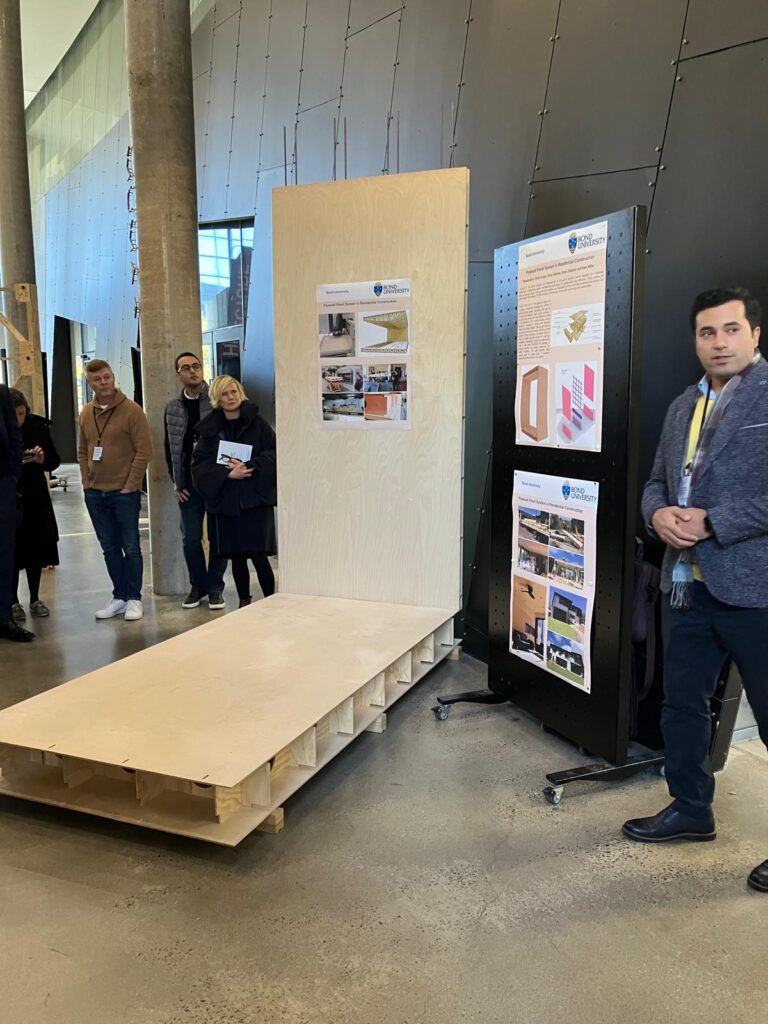
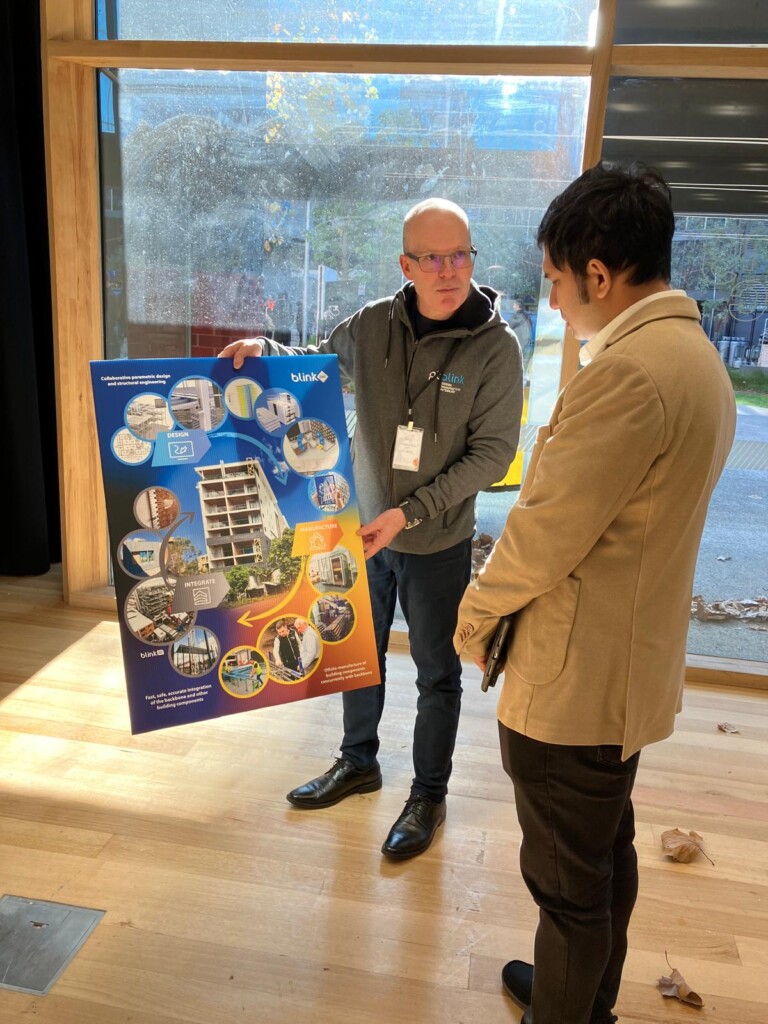
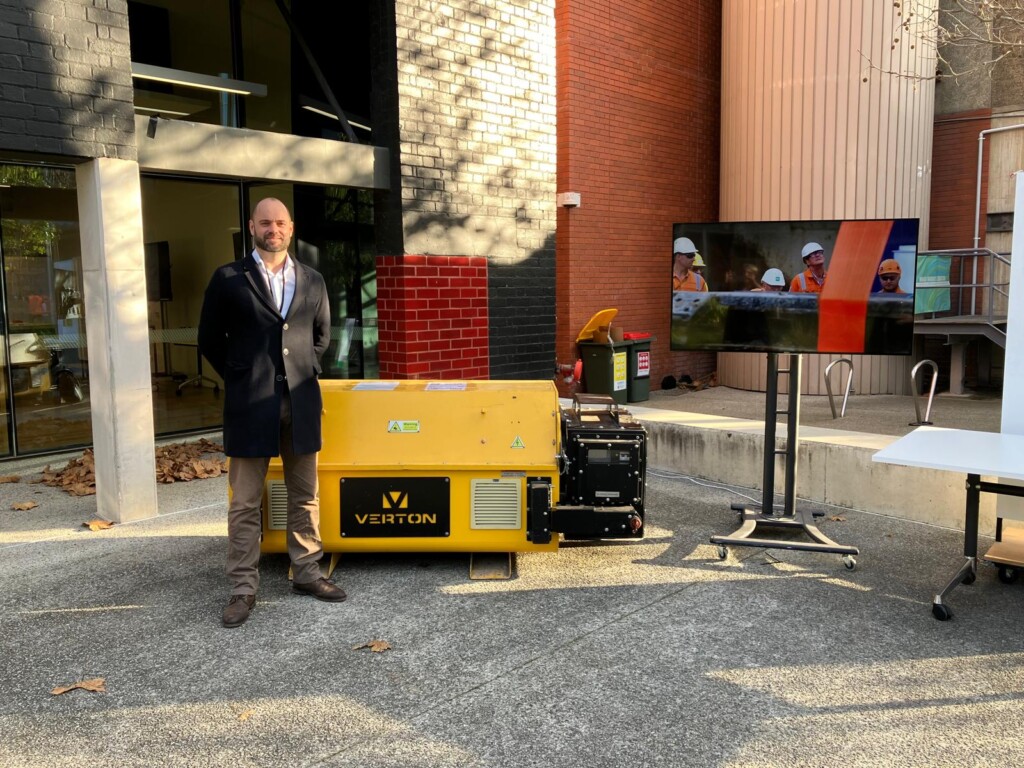
Future building industry leaders
The event was also an opportunity to introduce some of the building industry leaders of the future:
- For the University of Melbourne Backyard Futures – Movable Homes Studio, engineering students developed a relocatable small dwelling that demonstrates sustainable and efficient construction, and improves the aesthetics of social housing.
- For Monash University’s Building 2050 Studio, architecture students proposed a new ‘off-site construction hub’ in Fishermans Bend, including factories and public programs.
- RMIT University students developed the Same River Twice project, a future scenario of 6 (sub)urban blocks in Fishermans Bend that incorporates new planning controls, social housing and open space schemes and a plan for ‘character’ buildings.
- Monash Sustainable Buildings is a multidisciplinary student-run team that develops innovative solutions to the ongoing energy crisis, submitting each year to the US Department of Energy’s Solar Decathlon Design Challenge.
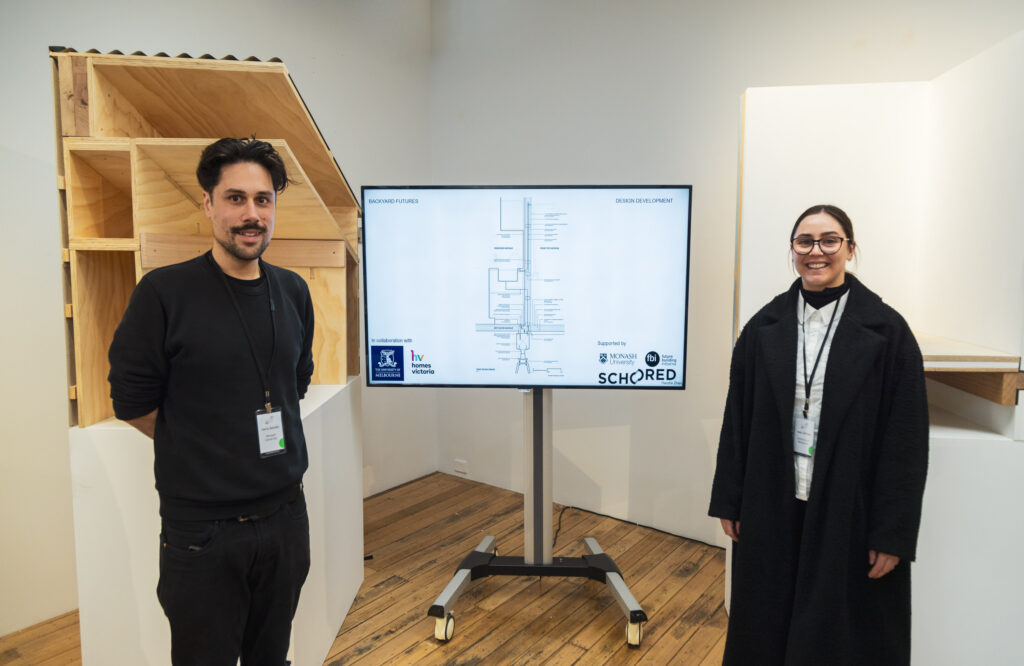
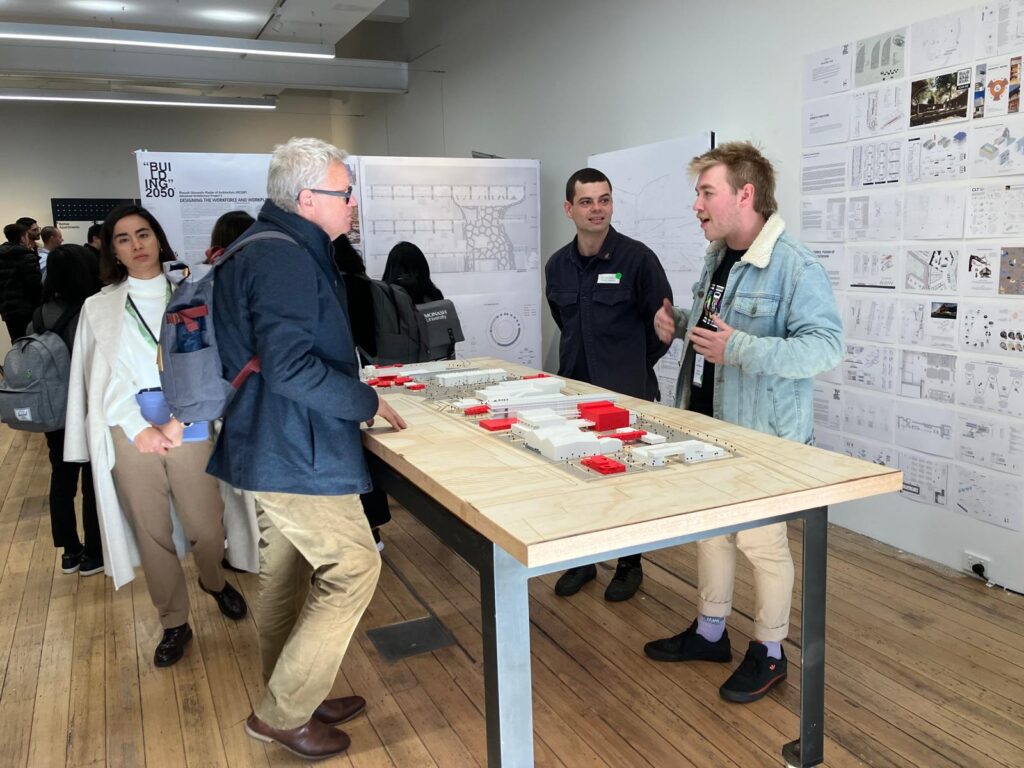
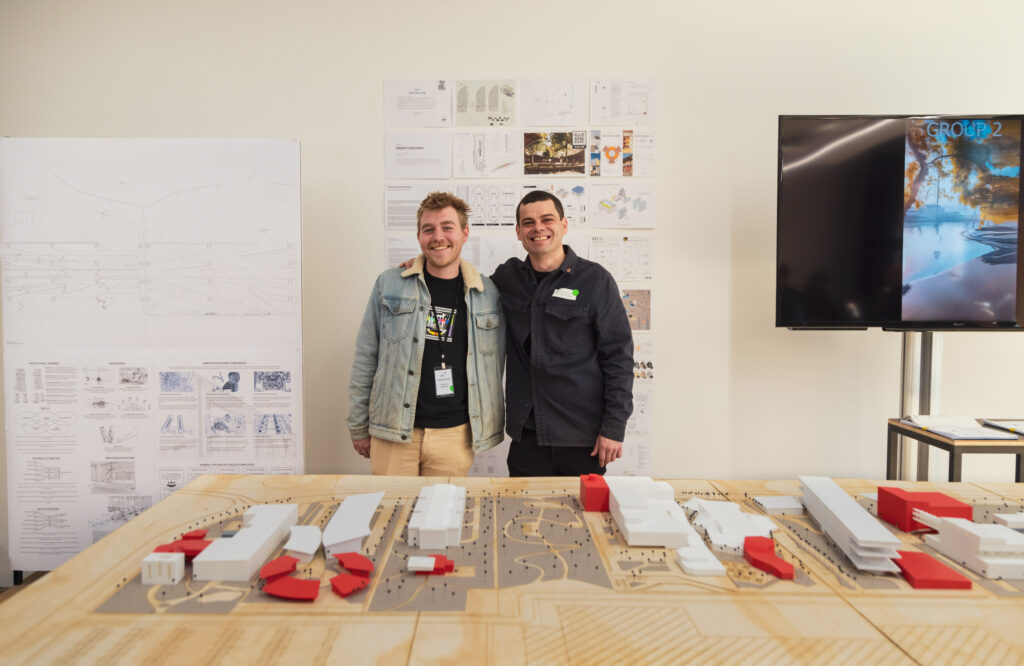
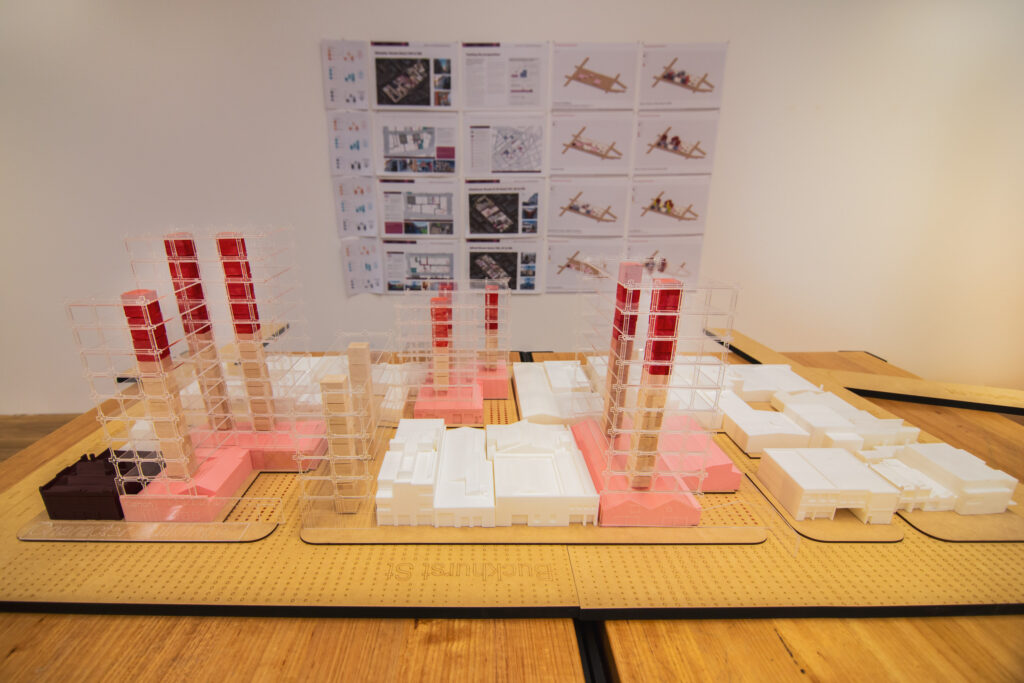
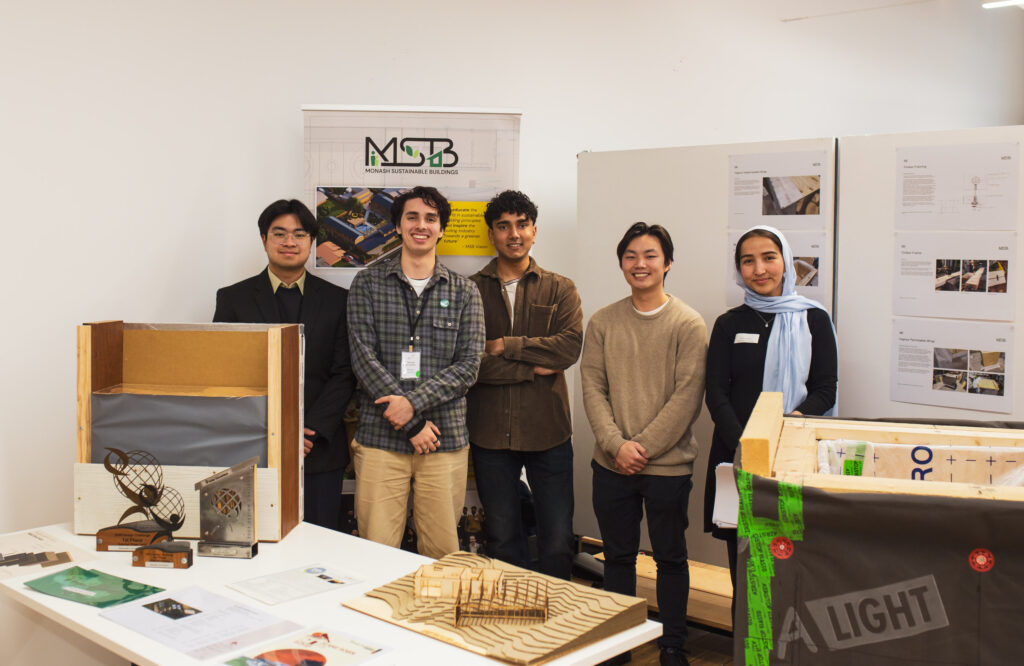
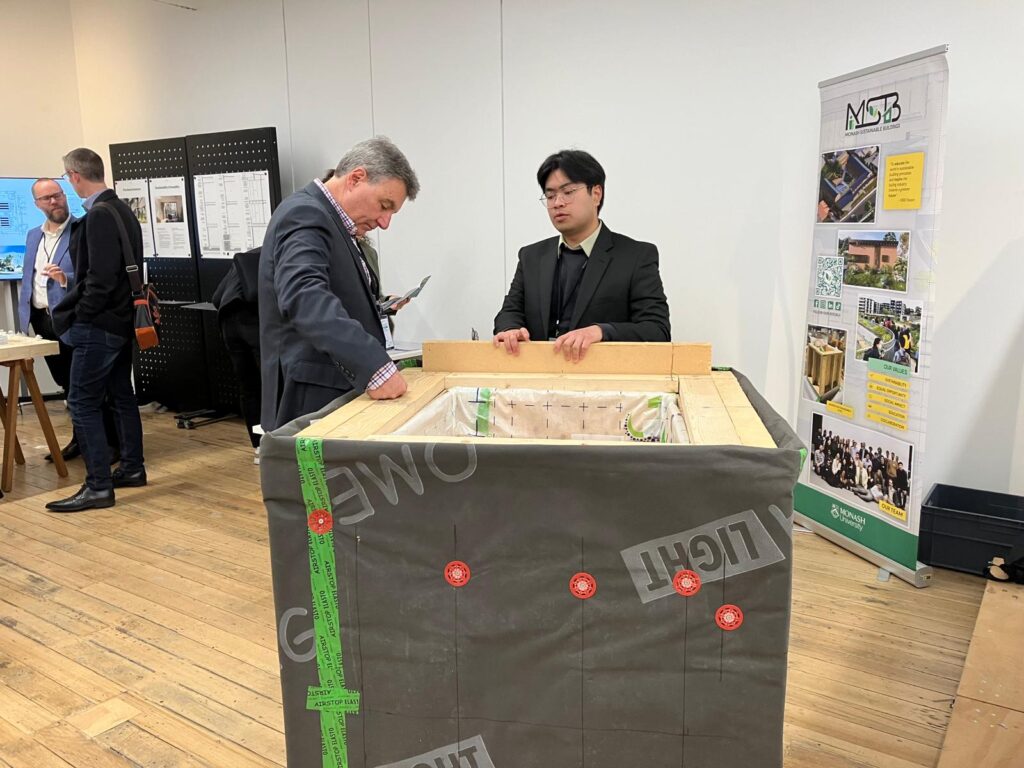